Visualize work site conditions through information collection and transfer
【Simplifying data logging and transfer】
Data accumulated in the FP7 can be transferred to a PC, making information easier to collect and therefore easier to trace.
Transfer electric power data from factories and offices to an FTP server on a regular basis.
|
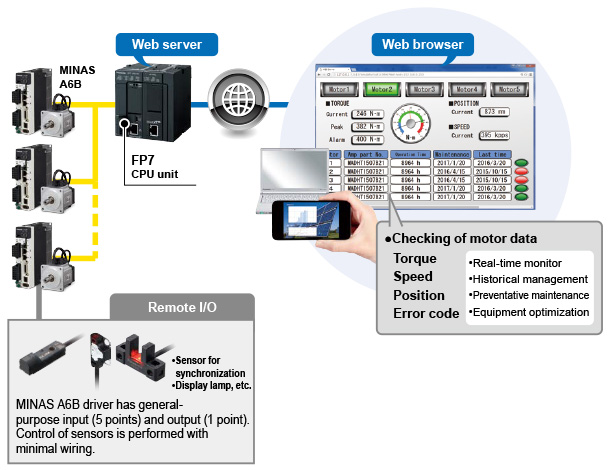 |
|
|
Manage your records by summarizing measurement data from your sensors together with result information from the inspection machines.
|
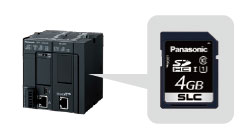 |
|
|
[FTPS Client function (SSL-compatible)]
The FP7 can generate and write data files to an FTPS server on a PC as well as read data files from the FTPS server.
|
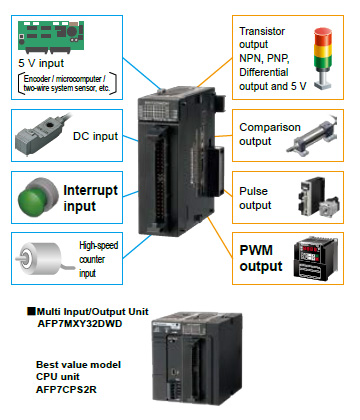 |
|
|
[FTP server function]
Allows the PC to read the logging data in the FP7's SD memory card and to write setting values and other parameters.
|
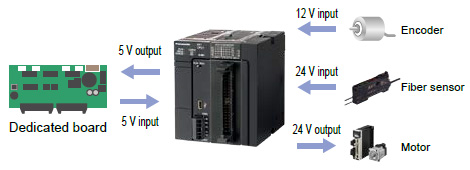 |
|
|
【Showing the current state of the work site】
The system's current state can be put on a web server for viewing with a browser.
Allow users from around the world to access the current state of their equipment.
|
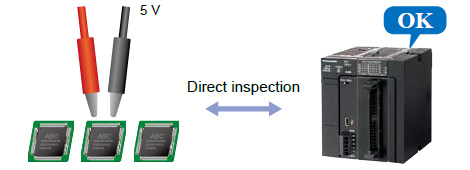 |
* The cloud server and web page need to be acquired separately. |
|
[HTTPS client function (SSL-compatible)]
Transfer data from the FP7 to a web server for easy viewing with a browser.
Send and receive data from multiple FP7 units on a schedule controlled by the FP7.
Communicate both inside the firewall on an intranet and outside the firewall to the wider world through the Internet.
|
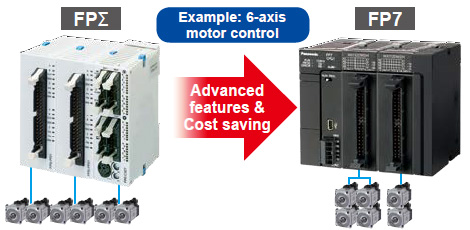 |
* The cloud server and web page need to be acquired separately. |
|
【Providing information by e-mail】
Information on the equipment's operational state along with daily and emergency reports are sent to users by e-mail.
Send the results and a notice of completion when a long-term test is completed.
|
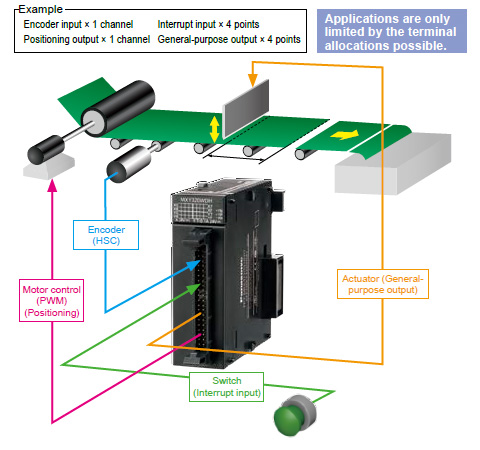 |
|
|
[E-mail sending function (SSL-compatible)]
Use instructions and timings controlled by the FP7 to send e-mails on a pre-set schedule or when a pre-set condition changes in the PLC. The e-mails can have data files attached and communication is SSL-capable to protect the e-mails.
|
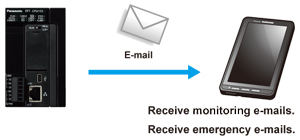 |
|
|
【Communicating with up to 220 devices】
Communicate easily with many units, including automation control devices like PLC and information devices such as PC.
Version information
These new functions are available with the following versions or later of the CPU unit and tool software.
Control FPWIN GR7: Ver. 2.3
CPU unit: Firmware Ver. 3.0
These new functions will be available by upgrading the firmware of the CPU units (Ver. 2.0 or later) released in December 2013.
Please contact us for details.
Compact design
The FP7 represents the top of the range of our PLCs and incorporates all the functionality and performance of a modular PLC in an outstanding compact format with a height of only 90 mm 3.543 in!
|
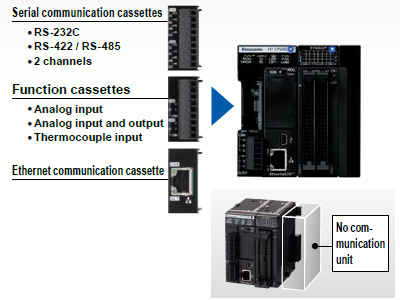 |
|
No power supply unit needed
No power supply unit is needed if the CPU is directly connected to DC power. Expansion units are clipped together without backplane.
・ Reduced costs
・ Smaller footprint
|
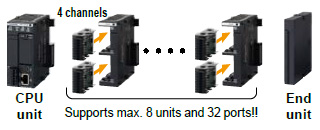 |
|
No communication unit needed
Enhancing communication features can be added using communication cassettes.
・ Reduced costs
・ Smaller footprint
|
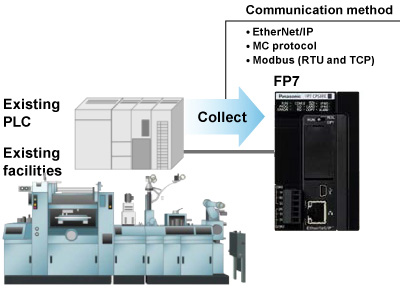 |
|
Local & remote connectivity
The FP7 is dedicated to the total integration into Web applications. The standard CPU boards with Ethernet interface offer connectivity without limits, from remote programming to monitoring and data logging to FTP server and Modbus TCP.
Data load to SD memory card from remote place
|
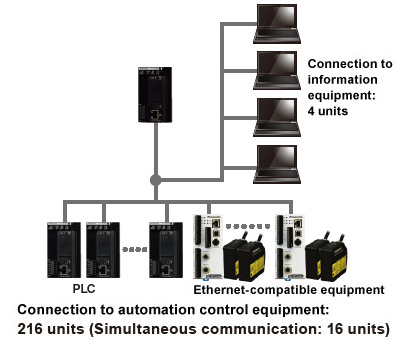 |
|
Security & reliability
The PLC programs can be password protected. Additionally, different security levels can be set, according to customer needs. The CPU unit can store two programs. In the event of fault, no SD memory card is needed to return to a previously saved backup program.
Built-in program backup
・ Production can resume in the event of fault
・ Original program is immediately to hand
|
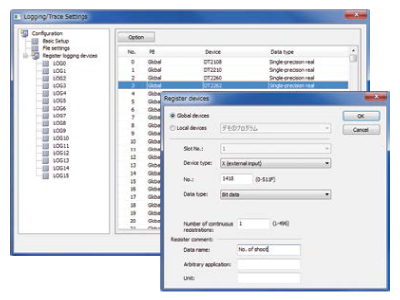 |
|
Update PLC program only after functional check
・ Operation can be tested on SD memory card
|
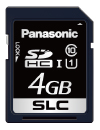 |
|
Return to top
Traceability
Operational and program editing events are logged. Automatic logs of program download and upload are useful, especially for program debugging.
Automatic recording of program change history
・ Useful for debugging
|
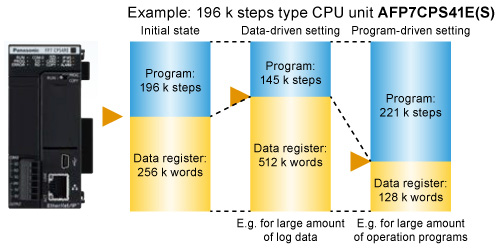 |
|
The log data stored on SD memory card.
・ Collection of traceability information
・ No logger unit offers lower costs.
|
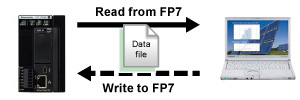 |
|
Return to top
Maintenance
The FP7 integrates several features that facilitate maintenance, diagnostics and troubleshooting. Set a maintenance schedule that is based on automatic measurement of contact switching cycles or overall ON time.
* Windows® is a trademark or registered trademark of Microsoft Corporation in the United States and other countries.
|
Hour meter operation
・ Indication of maintenance schedule for peripheral equipment
・ Indication of maintenance schedule for the PLC itself
|
|
Input contacts (X)
Automatically measures and logs total ON times and number of ON operations of connected sensors.
Output contacts (Y)
Automatically measures and logs total ON times and number of ON operations of connected actuators. The maintenance schedules for relays, motors, etc. can be optimized.
|
Return to top
Records the PLC's ON time
Equipment operating time can be estimated. You can decide which equipment to give priority to reactivate if more than one item of equipment is idle.
Data backup without battery
・ Simplified maintenance of equipment
|
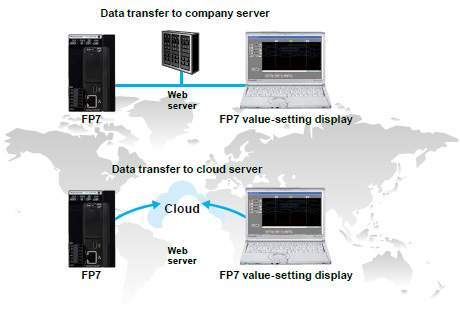 |
(Note 1): Clock / calendar operation can be held for about a week if the equipment is switched off. (Allow at least 30 minutes of quipment ON time.) |
|
Performance
The FP7 has a large memory capacity for program and data (up to 234 k program steps or up to 976 k data words) and a high-speed processor (11 ns/step). Control FPWIN Pro is (up-and downward) compatible with all Panasonic PLCs.
Shareable program and data memory
・ Both expandable when more capacity needed
・ No need to purchase upgrade models
|
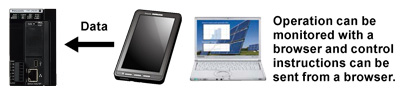 |
Note: For data register (DT), data up to 256 k words can be backed up. |
|
New analog units with high-speed DA and AD conversion
・ Conversion speed 20 times faster than in previous models
・ High-accuracy control
・ Noise-resistant with isolated channels
|
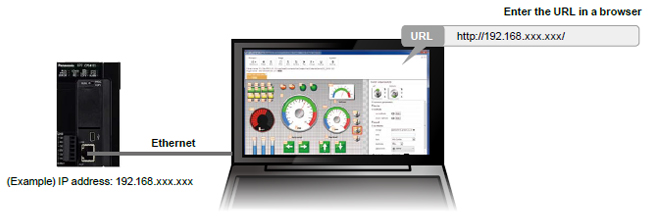 |
|
Advanced motion control (cam & gear)
FP7 programmable controllers are perfectly integrated with MINAS A5 servo drivers for accurate and sophisticated control in applications with up to 64 axes.
Besides, it is possible to set linear or sinusoidal acceleration and deceleration; startup/stop and speed changes are easy to accomplish in
applications with high inertia loads.
|
© 1993 - 2025 , PT Supra Engineering. All Rights Reserved.
| |